
With this new filament, it is possible to use the FFF method for different medical applications like dentures. PEEK filaments have been demonstrated for producing medical devices up to class IIa. It is technically feasible to process granular PEEK into filament form and 3D printing parts from the filament material using fused deposition modeling – FDM (or fused filament fabrication – FFF) technology. In the range of its melting temperature it can be processed using injection moulding or extrusion methods. PEEK melts at a relatively high temperature (343 ☌ / 649.4 ☏) compared to most other thermoplastics. Because of this and its low thermal conductivity, it is also used in fused filament fabrication (FFF) printing to thermally separate the hot end from the cold end. PEEK also performs well in high temperature applications (up to 500 ☏/260 ☌). PEEK seals and manifolds are commonly used in fluid applications. It is radiolucent, but it is hydrophobic causing it to not fully fuse with bone. PEEK is used in spinal fusion devices and reinforcing rods. PEEK is used in medical implants, for example in creating a partial replacement skull in neurosurgical applications.

It is one of the few plastics compatible with ultra-high vacuum applications, which makes it suitable for aerospace, automotive, and chemical industries. PEEK is used to fabricate items for demanding applications, including bearings, piston parts, pumps, high-performance liquid chromatography columns, compressor plate valves, and electrical cable insulation. It has high resistance to biodegradation. It is soluble in concentrated sulfuric acid at room temperature, although dissolution can take a very long time unless the polymer is in a form with a high surface-area-to-volume ratio, such as a fine powder or thin film. It is attacked by halogens and strong Brønsted and Lewis acids, as well as some halogenated compounds and aliphatic hydrocarbons at high temperatures. It is highly resistant to thermal degradation, as well as to attack by both organic and aqueous environments. The thermal conductivity increases nearly linearly with temperature between room temperature and solidus temperature. Some grades have a useful operating temperature of up to 250 ☌ (482 ☏). PEEK has a glass transition temperature of around 143 ☌ (289 ☏) and melts around 343 ☌ (662 ☏). Its Young's modulus is 3.6 GPa and its tensile strength is 90 to 100 MPa. The processing conditions used to mould PEEK can influence the crystallinity and hence the mechanical properties. PEEK is a semicrystalline thermoplastic with excellent mechanical and chemical resistance properties that are retained to high temperatures. The reaction is conducted around 300 ☌ in polar aprotic solvents - such as diphenyl sulfone. Typical is the reaction of 4,4'-difluorobenzophenone with the disodium salt of hydroquinone, which is generated in situ by deprotonation with sodium carbonate. PEEK polymers are obtained by step-growth polymerization by the di alkylation of bis phenolate salts. The polymer was first developed in November 1978, later being introduced to the market by Victrex PLC, then Imperial Chemical Industries (ICI) in the early 1980s. If you have any questions about PEEK or the processing of this material, please do not hesitate to contact us.Polyether ether ketone ( PEEK) is a colourless organic thermoplastic polymer in the polyaryletherketone (PAEK) family, used in engineering applications. We can produce various objects using our CNC turning and milling machines, tailored to your requirements and dimensions.
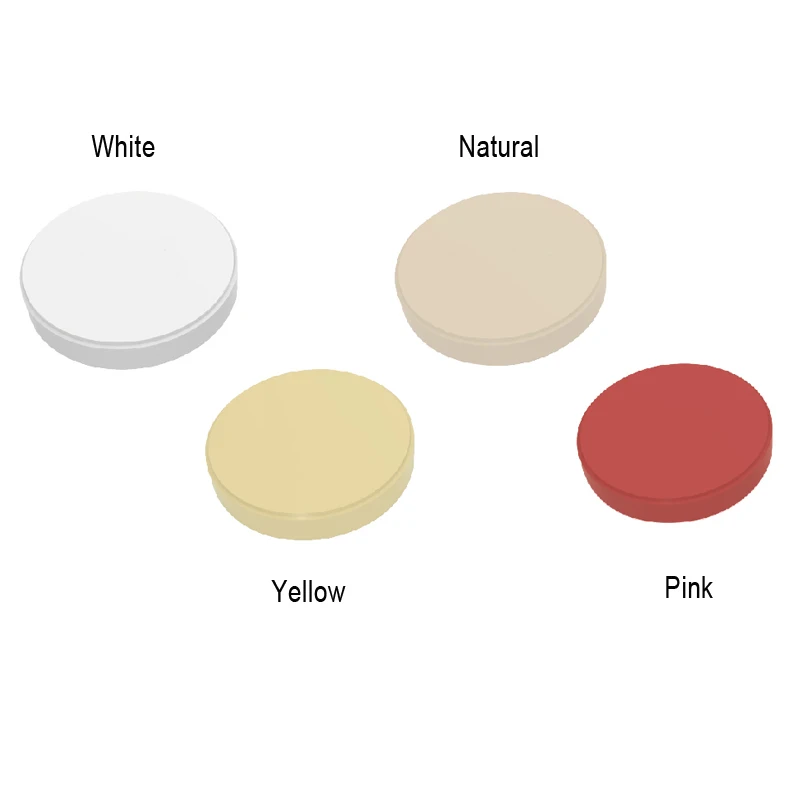
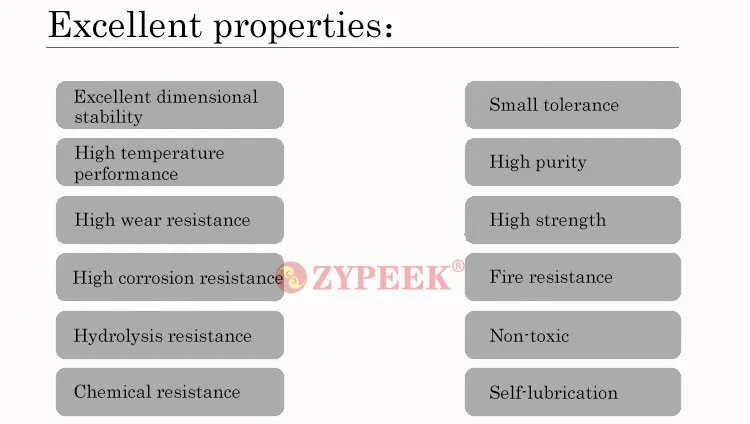
If you order PEEK from Induflex, the standard material is FCM. We will of course be happy to advise you.
#PEEK MATERIAL FULL FORM FREE#
Please feel free to contact us for advice or questions about additives and their effects. Please note that FCM approval does not apply for the above additives. PEEK with GF is not suited to loads and wear applications, since the material tends to grind on matt surfaces. Furthermore, glass fibre improves the crimp rigidity and dimensional stability.

It is possible to modify PEEK with the following additives:
